PCB Enclosure Design Guidelines and Standards
Key Takeaways
-
Understanding NEMA types is vital for aligning your PCB enclosure with the appropriate protection level for indoor or outdoor use.
-
Choose materials like ABS, polycarbonate, or metals based on durability, environmental conditions, and application needs.
-
Follow guidelines for uniform wall thickness, appropriate clearances, and tolerance considerations to prevent defects.
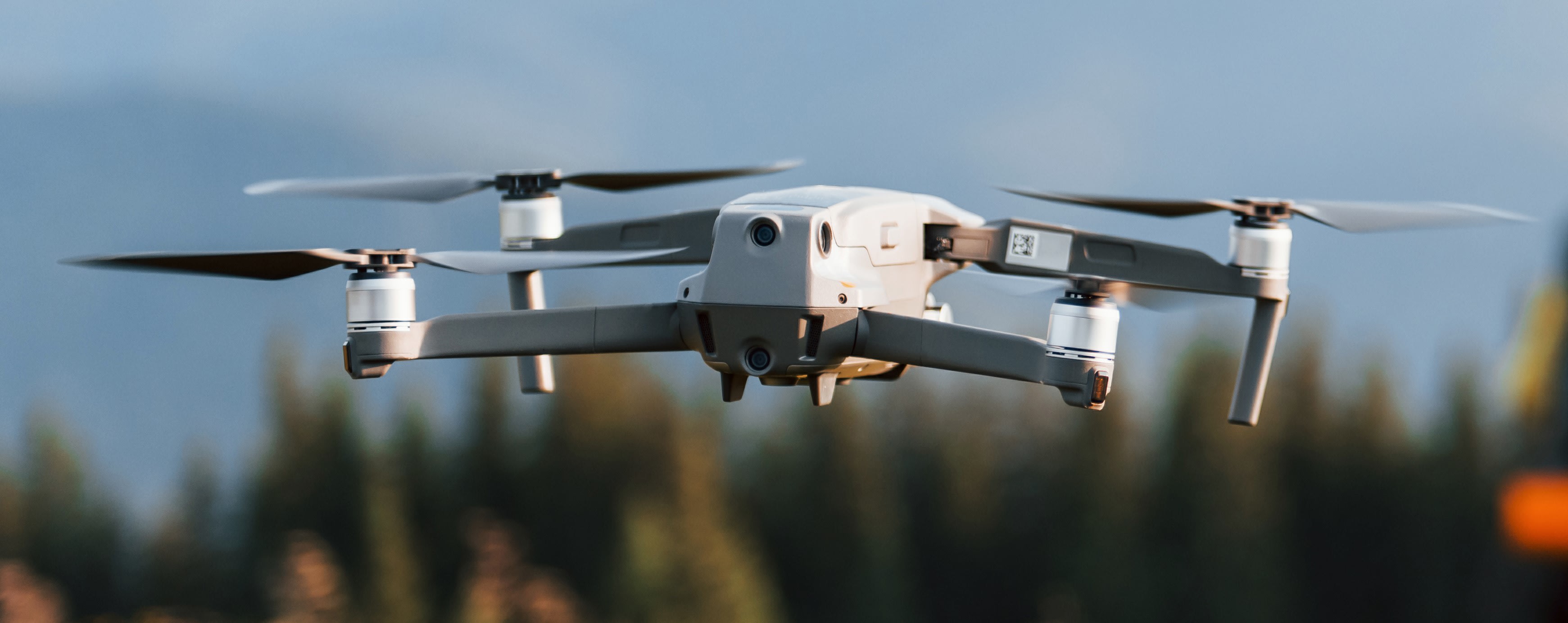
PCB enclosures are key to the success of many devices including consumer electronics such as drones.
Designing enclosures for devices can be complex due to the range of options. The type of enclosure depends on factors such as whether indoor or outdoor use, climate conditions, and operating temperature range. Since enclosures serve as the outer layer of a product—the part that users see and touch—they play a crucial role in product development. It's essential to follow PCB Enclosure design guidelines to make enclosures practical, durable, visually appealing and user-friendly.
PCB Enclosure Types
Enclosures should provide shock absorption to keep the board stable, support efficient heat dissipation, and not be relied upon for fixing EMI issues, as those are best addressed during the board's design phase.
Especially if you’re targeting a commercial project, starting the design process with an understanding of desired enclosure capabilities is important. Fortunately, the National Electrical Manufacturers Association (NEMA) outlines eight specific categories for PCB enclosures, with, Types 1, 3, 4, and 4X the most frequently used.
NEMA Enclosure Type |
Enclosure Type Description |
NEMA 1 |
|
NEMA 3 |
|
NEMA 4 |
|
NEMA 4X |
|
NEMA 6, 6P, and 7 |
|
NEMA 12 |
|
PCB Enclosure Design Guidelines for Materials
The choice of PCB enclosure materials depends largely on the NEMA standards. Indoor enclosures, like those classified as Type 1 and 12, are usually made from materials such as polycarbonate, polyester, or ABS plastic. In contrast, outdoor enclosures, including Types 3, 4, 4X, 6, 6P, and 7, are typically constructed from metals. Common metals for these outdoor enclosures include aluminum, cold-rolled steel, stainless steel, galvanized steel, and copper. Commonly used plastics include:
-
ASA and PC blend: Features enhanced high-temperature performance, impact strength, and offers resistance to chemicals and weather.
-
ABS: Commonly used due to its balanced properties for electronic enclosures; good chemical resistance but sensitive to prolonged sunlight exposure.
-
Polycarbonate (PC): Popular for its toughness, thermal stability, UV resistance, and transparency; suitable for indoor and outdoor use but not ideal for strong alkaline (high-PH) substances.
-
PC and ABS blend: Offers high impact strength, resilience at low temperatures, and good chemical resistance; best for indoor use.
-
PPE/PPO (Polyphenylene Ether/Polyphenylene Oxide): Known for its excellent mechanical, thermal, and electrical properties; best for indoor use due to UV sensitivity.
Commonly used metals include
-
Aluminum: Lightweight, corrosion-resistant, and can be anodized for extra durability; alloys 5050 (good for sheet metal) and 6061 (machinable but not bendable) are commonly used.
-
Cold-rolled steel: Cost-effective with good stiffness and durability; suitable for indoor use when powder-coated, but lacks inherent corrosion resistance.
-
Stainless steel: High strength and corrosion-resistant; can be left bare or powder-coated for a brushed finish.
-
Galvanneal: Low-carbon steel with a zinc coating bonded to resist flaking; more durable than cold-rolled steel in wet environments, but less so than stainless steel or aluminum.
Enclosure Thickness and Shape
Fused Deposition Modeling (FDM) is a widely used 3D printing technique that primarily utilizes thermoplastic materials, although it can also be adapted to print with some metal filaments. It builds objects layer by layer by extruding melted material through a nozzle.
Injection molding, on the other hand, is a manufacturing process that involves injecting molten material into a mold to produce parts. While it is most commonly used with plastics, metals can also be injection molded using a specialized technique known as metal injection molding (MIM).
For both plastic and metal, maintaining uniform wall thickness in the design is crucial to ensure that the material flows evenly through the mold, reducing the risk of defects. Features like fileted corners, edges, ribs, and gussets can further enhance the strength and stability of the molded part.
Enclosure Clearance Requirements
Each manufacturing method requires allowances for shrinkage and distortion, and PCB enclosures are no exception.
-
To account for machine tolerances, it’s recommended to include a safety clearance of around 0.5mm in the enclosure design.
-
For areas around ports and holes, a clearance of 0.2mm to 0.3mm is advisable.
One common issue in enclosure design is components getting stuck due to these variations. To prevent this, it's a good idea to create 3D models of the components and incorporate the necessary clearances. If you're handling prototyping and manufacturing in-house, conducting tolerance tests with your equipment can help ensure the enclosure fits as intended.
Other standards
Depending on your desired application, utilizing standards is a good way to ensure you adhere to the PCB enclosure design guidelines right for your project.
Category |
Standard/Details |
IP Ratings |
|
UL Certification |
|
IEC Standards |
|
Other Considerations
Depending on your project, your device or rack may require some of the following:
-
Cable Management: Bushings, clips, and clamps protect and organize cables, preventing short-circuits and managing thicker cables efficiently.
-
Mounting: Wall-mounts save space and are easy to install, while floor-mounts offer stability but less flexibility.
-
Accessories: Features include security locks, temperature monitoring, cooling vents, and mounting aids.
-
Finish: Options include durable polyester urethane powder, corrosion-resistant electrocoat, and tough epoxy powder with reduced UV durability.
OrCAD X for PCB Design Enclosure
One of the most important elements of PCB enclosure is actually ensuring that you adhere to the design guidelines set by the standards and features you require. For this reason, utilizing a robust PCB design software like OrCAD X is essential.
OrCAD X Capability |
Description |
Cross-Section Editing |
Provides tools for setting up PCB stack-ups, adjusting layer parameters like thickness and material, and managing design constraints essential for designs that fit tight enclosures. |
3DX Engine |
Allows for visualizing designs in a 3D environment, creating a better assessment of how PCBs fit within enclosures. Helps with assembly planning and mechanical error reduction. |
3D Export Capabilities |
Facilitates the export of 3D data in multiple formats for use in MCAD systems, improving ECAD-MCAD collaboration and ensuring that the PCB design integrates well within its enclosure. |
Design for Manufacturing (DFM) Checks |
Provides checks for fabrication, assembly, and testing to identify potential manufacturing issues early in the design stage, reducing costly iterations. Useful for ensuring that the enclosure design accommodates manufacturing constraints. |
Constraint Manager |
Offers a comprehensive tool for setting and managing electrical, physical, and spacing constraints. Ensures that PCB design elements stay within specified limits, which is crucial for fitting into predefined enclosure dimensions. |
With Cadence's suite of tools, particularly OrCAD X, you gain powerful features like 3D visualization, cross-section editing, and comprehensive design checks to ensure your enclosure meets industry standards for safety, durability, and functionality. For more information on how Cadence's tools can elevate your design, visit our PCB Design and Analysis Software page and explore the capabilities of OrCAD X.
Leading electronics providers rely on Cadence products to optimize power, space, and energy needs for a wide variety of market applications. To learn more about our innovative solutions, talk to our team of experts or subscribe to our YouTube channel.