Standard PCB Thickness and Optimization
Key Takeaways
-
Designers may want to adhere to standard PCB thicknesses for board edge connectors and manufacturer compatibility.
-
However, board design with weight as a mission-critical factor can benefit from non-standard thicknesses.
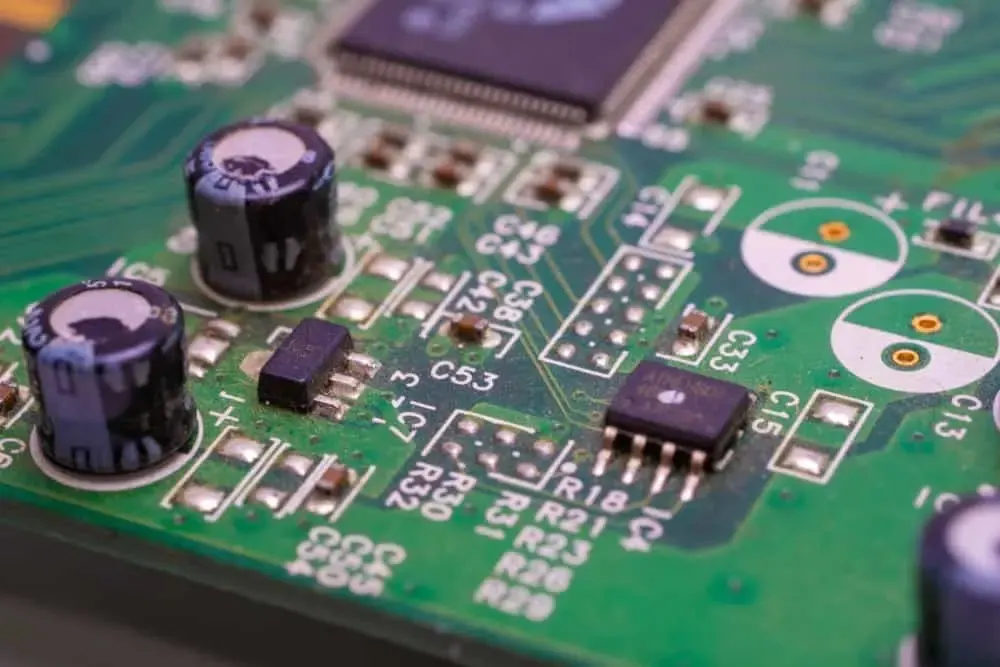
Layer count, stackup configuration, and current capacity determine PCB thickness.
After designing the stackup to ensure the correct impedance structures for the various board layers, some designers may pay no heed to the board thickness. After all, engineering design documents guide this aspect of the design, and the layout focuses on the electrical aspects of the board rather than the physical characteristics (so long as this doesn’t affect mating, enclosure mounting, etc.)
Designers should be aware that standard PCB thicknesses, though common for a reason, are more a convention than a standard, offering an additional angle of modularity and optimization that can realize significant cost savings on high-volume production lots.
Should I Use a Standard PCB Thickness?
Yes |
Maybe |
No |
|
|
|
Standard PCB Thickness
In some aspects, PCB board thickness reflects the board's complexity – designers shouldn’t expect to fit a layer count well into the double digits within the standard 62 mil/1.57 mm thickness.
Standard PCB Thicknesses Summarized
|
Most low- to moderate-layer count PCBs adhere to traditional thickness standards for manufacturing consistency, reflecting early Design for Manufacturability (DFM) practices. Initially, electronic assemblies used nonconductive 1/16-inch plywood breadboards. As multi-board systems developed, designers sought to reduce inter-board connections. The presence of conductive surfaces on PCBs enabled simpler connectors, leading to the creation of edge connectors where one board functions as a plug.
Copper Thickness and Its Impact
Measured in ounces per square foot, standard copper weights include 1 oz, 2 oz, and 3 oz layers. Thicker copper handles higher currents and improves heat dissipation but increases the PCB's overall thickness. For high-power or power distribution boards, copper can reach up to 6 oz, necessitating base material adjustments to maintain mechanical stability.
Tolerance and Industry Standards
PCB thickness tolerance is typically ±10%, crucial for proper fit and electrical performance. Industry standards like IPC-2221 guide thickness selection based on layer count, copper weight, and thermal factors. Adhering to these standards ensures consistent manufacturing and compatibility with electronic components, leading to reliable and repeatable PCB designs.
Design Determines Thickness
Design requirements and constraints take precedence over standard manufacturing practices, and reputable manufacturers will collaborate with designers to meet specifications, provided the thickness isn't extreme, which could increase costs due to yield issues.
Excess thickness raises material costs and complicates manufacturing, as processes are optimized around the 62 mil standard. Extremely thin, rigid PCBs may face production challenges.
Additionally, substrate thickness affects dielectric properties and impedance, impacting signal integrity. Surplus material also affects more than costs: applications like aerospace require weight reductions, and high-vibration environments benefit from thinner boards for enhanced reliability.
Determining An Appropriate Board Thickness
More than ever, board dimensions and features are customizable to meet the circuit's electrical needs and the enclosure's physical requirements. As form follows function, the best step is for designers to begin at the lowest level of design and work their way up:
Factor |
Description |
1. General circuit density |
|
2. Board-edge connectors |
|
3. Enclosure design |
|
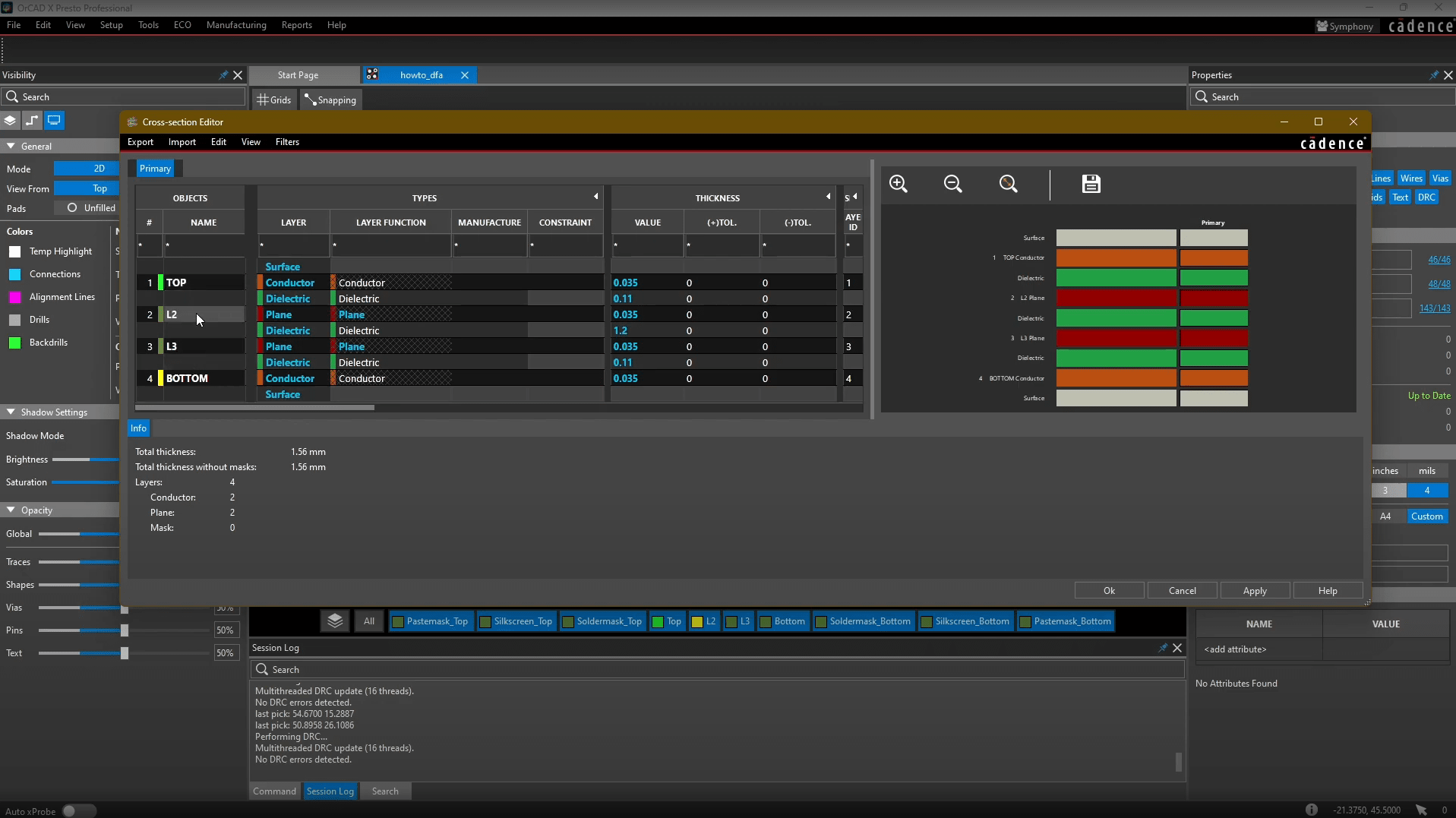
OrCAD X cross-section editor allows for customizing layer thickness and more.
Cadence Offers Solutions Through Thick and Thin of Board Design
The OrCAD X Cross-Section Editor offers capabilities for designing optimal PCB thickness and connector configurations. Designers can easily configure the PCB stack-up by adding or removing layers, setting precise thicknesses, and selecting appropriate materials and surface finishes for each layer.
The editor supports both rigid and rigid-flex designs, providing visual previews of multiple stack-ups and via paths to ensure seamless integration. Users can switch measurement units between mils and millimeters to match project specifications and manually adjust layer tolerances for accuracy.
Additionally, cross-section technology files are imported and exported, facilitating the reuse and sharing of standardized stack-up configurations across different projects. By enabling the definition of plane layers and managing layer types, the Cross-Section Editor helps streamline the process of choosing the right board thickness and connector design, ensuring that PCB layouts meet mechanical, electrical, and cost requirements efficiently.
Optimizing PCB thickness is crucial for achieving the right balance between performance, durability, and cost. Designers can leverage OrCAD X, to efficiently manage and customize PCB thickness. Discover more about how Cadence tools can enhance your PCB design workflow by visiting our PCB Design and Analysis Software page and explore the full capabilities of OrCAD X today.
Leading electronics providers rely on Cadence products to optimize power, space, and energy needs for a wide variety of market applications. To learn more about our innovative solutions, talk to our team of experts or subscribe to our YouTube channel.