High Voltage PCB Design Guidelines
Key Takeaways
- Proper trace spacing and creepage are vital to avoid high voltage flashover, arcing, and insulation failures.
- Choose dielectric materials with high CTI ratings to minimize creepage distances and ensure durability in high voltage environments.
- Isolate high voltage components and follow IPC-2221 and IEC 60950 standards to maintain safe clearance and prevent arcing.
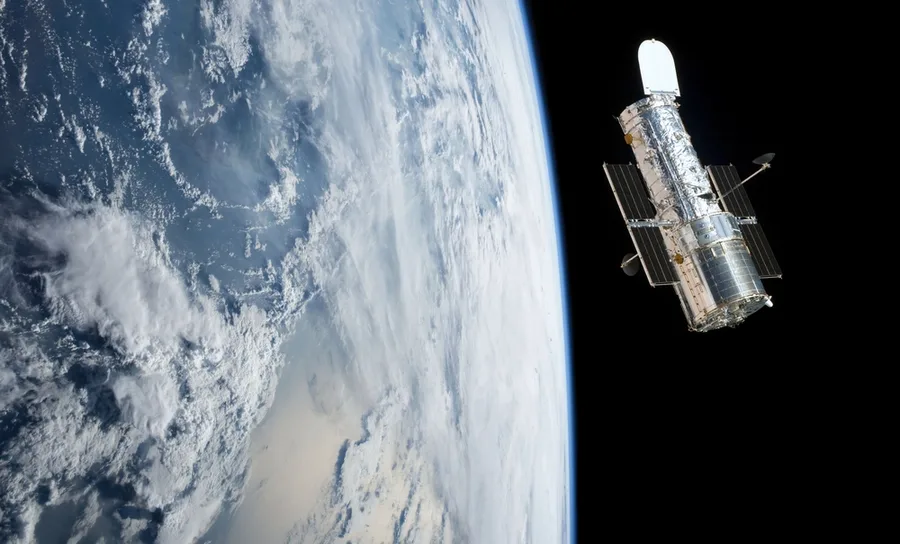
NASA has experienced issues with their high voltage spacecrafts in the past.
NASA experienced performance issues with 1.5 kV power supplies in spacecrafts like the Hubble and Cassini Telescopes due to initial design flaws, including narrow part parameters, insulation issues, and incorrect materials. As a 2006 report stated, “Designers did not take the high voltage problems seriously in the initial design.”
For today's high-density layouts and demanding applications, a rigorous approach to high voltage PCB design guidelines is crucial. This involves understanding insulation, board materials, clearance, creepage, and the impact of environmental factors like altitude while adhering to relevant industry standards.
High Voltage Design Begins with the PCB Layout
In high voltage PCB design, proper trace spacing maintains signal integrity and helps prevent the propagation of electromagnetic interference. If we rightfully consider the board as a series of conductive elements, the possibility of differences in potential creating high voltage flashover with narrow trace spacing becomes a certainty.
While a high voltage design doesn’t always have to be a power grid, you’ll want to be wary when dealing with any electrification designs.
High Voltage PCB Standards
In addition to the IPC-2221 standard by the Association of Connecting Electronics Industries (IPC), which sets the design principles for interconnections on printed circuit boards (PCBs), there are also the IEC/UL 60950-1 standards by the International Electrotechnical Commission (IEC) and Underwriters Laboratories (UL). These standards focus on the "safety of information technology equipment" and outline the minimum spacing requirements for PCBs. Together, these standards provide guidelines for high voltage PCB design, emphasizing two key parameters: clearance and creepage.
High Voltage Fundamental: Clearance and Creepage
Two of the most critical parameters in high voltage PCB design are clearance and creepage, as defined by standards like IEC/UL 60950-1 and IPC-2221.
- Clearance: This is the shortest distance through air between two conductive parts or between a conductive part and the bounding surface of the equipment. Insufficient clearance can lead to arcing or flashover, especially as voltage increases or environmental conditions (humidity, dust, altitude) decrease the breakdown voltage of air.
- Creepage: This is the shortest path along the surfaceof an insulating material between two conductive parts. Contamination or moisture on the PCB surface can create conductive paths, and creepage distance is designed to mitigate this risk.
Clearance and Creepage Guidelines
Guideline |
Details & Information |
---|---|
Trace Spacing |
- Follow IPC-2221 and IEC/UL 60950-1 standards. - Narrow spacing increases flashover risk. - Higher voltages require greater spacing to prevent dielectric breakdown. |
Clearance |
- Shortest air distance between conductive parts. - Follow IEC 60950 and IPC-2221B based on voltage, humidity, and pollution levels. - Critical to prevent arcing. |
Creepage |
- Distance measured along the surface of insulation. - Refer to IPC-2221A/B standards. - Use slots or barriers to increase creepage. - Adjust for voltage and environmental conditions. |
High Voltage Design Through Material Selection
Materials used in high voltage PCBs must offer high dielectric strength, high resistivity, and a low power factor to minimize arcing, heating, and thermal breakdown. Additional key properties include tensile strength, hardness, surface breakdown strength, thermal expansion, chemical resistance, and long-term stability against aging and oxidation.
High voltage insulation may involve functional insulation for circuit operation and protective insulation to prevent breakdown or electric shock. Common materials include encapsulating resins, conformal coatings, and solid insulating barriers. Where human contact is possible, regulatory standards mandate additional insulation layers for safety.
Material & Layout Considerations
Guideline |
Details & Information |
---|---|
Sharp Corners in Layout |
- Avoid sharp edges that cause electric field concentration. - Prevents insulation failure and flashover. |
Material Selection |
- Choose materials with high dielectric strength and CTI. - FR-4 may not be suitable for very high voltages. - Use encapsulating resins or coatings for added insulation. |
Conformal Coatings |
- Acrylic or silicone coatings improve creepage and resist moisture. - Important in humid environments. - May impact thermal characteristics. |
Slots, Cutouts, & Isolation Slots |
- Use slots to increase creepage between high voltage traces. - Add isolation slots between high and low-voltage nets. |
Ground Planes & Grounding |
- Use solid ground planes for EMI and safety. - Avoid placing under high voltage traces to reduce arcing risk. - Proper grounding improves signal integrity. |
Silkscreen and Labels |
- Mark high-voltage areas with durable labels or symbols. |
Surface Finish |
- Use ENIG or silver to prevent oxidation. - Some finishes may lower dielectric strength or reduce creepage distance. |
Selecting Dielectric Materials
When selecting dielectrics and insulators for a PCB, use the comparative tracking index (CTI) to determine which material is best. The CTI is the maximum voltage measured in volts at which a material withstands 50 drops of contaminated water without forming conductive paths because of electrical stress, contamination, or humidity.
- Manufacturers use the CTI to compare the performance of insulating materials under wet or contaminated conditions.
- Materials that have a high CTI value have a lower required minimum creepage distance and allow a shorter distance between two conductive parts. The shorter distance allows the use of high-density circuits in a high voltage environment.
CTI Standards
The Comparative Tracking Index (CTI) is a critical property used to classify insulating materials based on their resistance to electrical tracking, which can occur due to moisture and contamination. A higher CTI value indicates greater resistance to tracking and allows for shorter creepage distances in high voltage designs.
According to UL 746A, materials are divided into four material groups based on their CTI ratings. These groups help determine the minimum required creepage distances for safety and compliance with design standards like IEC 60664 or IPC-2221. When referencing the table below, keep in mind the materials in Material Group I have the highest tracking resistance, making them preferable for high voltage or high-humidity applications.
Material Group and Associated CTI Rating
Material Group |
Rating |
---|---|
I |
600 volts </= CTI |
II |
400 volts </= CTI < 600 volts |
IIa |
175 volts </+ CTI < 400 volts |
LLb |
100 volts </+ CTI < 175 volts |
Design Guidelines for Dielectrics
Although FR4 laminates have a high breakdown voltage, the weaker structure and porosity of FR4 can allow the material to become prone to contamination and a lessening of the dielectric value. Because of FR4 limitations, high voltage laminates that have a non-conductive base layer and prevent arcing serve as the gold standard for high voltage circuit design. High voltage laminates have higher levels of resin and glass than standard board materials.
Working within high voltage circuit boxes becomes easier when you design them properly.
High Voltage Design Guidelines For Component Selection
High voltage circuits rely on both passive and active components:
- Resistors in high voltage circuits require low inductance and low-temperature coefficients.
- Ceramic capacitors must have high resistance, high-temperature coatings, and dielectrics that can withstand high voltages. These capacitors should maintain stable electrical parameters across a wide range of applied DC voltages and under various environmental conditions.
- Semiconductor devices for high voltage circuits include MOSFETs, IGBTs, MOS-controlled Thyristors, Power FETs, and SCRs, which must follow manufacturer guidelines for not exceeding values that can destroy the devices. For example, high voltage circuits may require components that have higher breakdown voltage ratings and the capability to handle higher currents.
Component-Level Considerations
Guideline |
Details & Information |
---|---|
Copper Thickness |
- Use thicker copper for high-current paths. - Ensure the copper surface is smooth to prevent arcing. |
Resistors and Capacitors |
- High voltage resistors should have low inductance and temperature coefficients. - Provides safety margins; components should exceed the highest voltage they will encounter in operation. |
Thermal Management |
- Use heat sinks and thermal vias to maintain airflow and cooling pathways. - Prevents overheating and extends component lifespan. |
Circuit Design for Transients |
- Shield cables and optimize routing to reduce surges. - Protects sensitive components from voltage spikes and EMI. |
Controlled Impedance |
- Use impedance-matched routing for high-speed signals. - Maintains signal integrity and reduces reflections. |
Following High Voltage PCB Design Guidelines with OrCAD X
High Voltage Design Guideline |
OrCAD X Features |
Trace Spacing |
Constraint Manager: Allows setting up custom spacing rules for high voltage traces. Use the Constraint Manager to create spacing rules for nets and apply these for trace widths and gaps to meet high voltage standards. |
Clearance |
3D Visualization & Clearance Checks: OrCAD X features an interactive 3D engine to visualize clearance between parts. |
Creepage |
Design Rule Checks (DRC): OrCAD X performs comprehensive DRCs, including creepage distance checks based on IPC-2221B standards to prevent flashover on high voltage paths. |
Layer Placement & Stackup |
Cross-Section Editor: OrCAD X supports setting up a customized stack-up with specific dielectric thicknesses and layer placement to isolate high voltage components. |
Successfully navigating high voltage PCB design guidelines demands meticulous attention to detail, from material selection and component ratings to precise clearance and creepage calculations. OrCAD X provides an integrated environment with tools like the Constraint Manager for defining specific high voltage rules, DRC for verification against standards, and a robust layout editor for implementing isolation techniques. Try OrCAD X for free, or explore the full OrCAD X platform to leverage its comprehensive features for your design challenges.
Leading electronics providers rely on Cadence products to optimize power, space, and energy needs for a wide variety of market applications. To learn more about our innovative solutions, subscribe to our newsletter or our YouTube channel.