Controlled Impedance Routing for Signal Integrity
Key Takeaways
-
Controlled impedance routing prevents signal distortion by matching trace impedances to preserve signal integrity.
-
Proper impedance matching of both components and traces is vital for high-speed PCB design.
-
The choice of PCB material, such as low-loss laminate, plays a significant role in minimizing signal degradation.
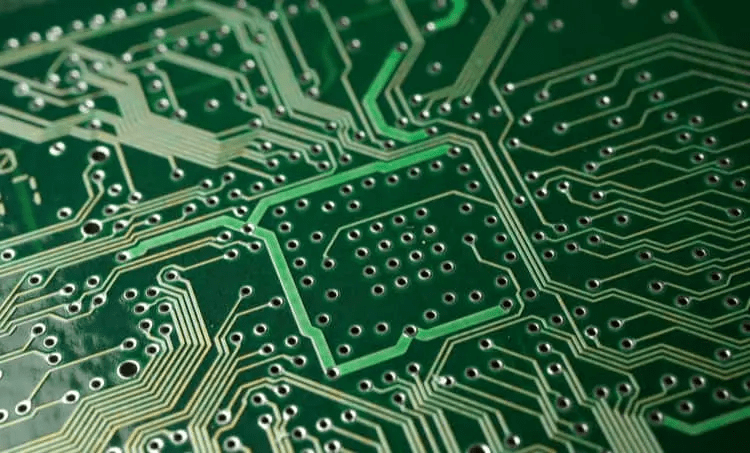
To achieve signal integrity in circuits, we follow practices such as avoiding right-angle bends, separating clock signals and power signals, and maintaining the shortest distance between components. When end-users are concerned about signals and their quality, they are often not aware of the back-end design modifications made to protect signal integrity.
Controlled impedance routing in circuit boards configures the dimension of the routes to match a specified characteristic impedance. This approach is used to control the impedance of the routes by changing their dimensions and environment so that the signal traveling through them retains the proper signal integrity characteristics.
As the speed of a signal increases—even from GHz range with a smaller footprint area—signal integrity is often a major consideration. Controlled impedance routing is a method to assure signal integrity and help preserve the signal strength until it reaches the destination point from the source.
How Controlled Impedance Routing Behaves In a Circuit
In a circuit, there will be a lot of components other than the source and the load. The energy from the output pins of components flows towards the load through traces, but with distortions and losses. In certain cases, the energy that is not absorbed by the load reflects back to the source side and causes additive or subtractive effects and results in ringing. The signal integrity of the circuit is compromised in all these conditions.
When the signal integrity is compromised, the circuit may start to behave in unexpected ways. The reflection of the signals back to the source side can be prevented by matching the impedances of the traces.
Within circuit boards power is propagated along the length of the trace. The power transferred is maximum when the source and load impedances are matched. The impedance matching couples the energy from the source to the routing and from routing to load.
Considering the criteria of impedance matching during the routing of a circuit is called controlled impedance routing. This technique prevents distortions, ringing, and loss of signal in circuit boards. |
Designing Controlled Impedance Routing
Controlled impedance routing in circuit boards is done in two steps:
-
Impedance matching of components
-
Impedance matching of traces
Impedance Matching of Components
The first step of controlled impedance matching is to match the impedances of the components in the circuit. The high impedance of input pins and the low impedance of output pins leads to impedance mismatch. Including termination components between the input and output pins matches the impedance of the components.
Impedance Matching of Traces
In this step, the routing of the circuit traces is done to achieve the required impedance. The characteristic impedance of the traces is dependent on the resistance, inductive reactance, capacitive reactance, and conductance. The geometry of the length, width, and thickness of the trace determines the impedance, and changing the dimension is one method to achieve impedance matching.
If the board is designed with controlled impedance routing, the impedance remains constant throughout the trace from source to load, even when it passes through different layers. Typical impedance values of the traces range from 25 to 125 Ω.
The PCB material dielectric constant and dielectric thickness also influences the impedance of the traces. The selection of PCB material is a criterion to match the impedance. For high-speed board designs, the laminate material of low dielectric constant and low loss tangent is preferable. This enhances the signal performance and minimizes the signal distortion and phase jitters. A PCB fabricated in low loss material improves the signal integrity of high-frequency designs.
Examples of Controlled Impedances in PCBs
In multilayer circuit boards, the traces are between the layers, so the thickness of the laminate material on either side of the trace is considered for impedance matching. The following are some examples of controlled impedances in multilayer PCBs:
Type of Microstrip |
Description |
Embedded Microstrip |
The trace is sandwiched between the planes, with a plane on one side and laminate on either side, followed by air. |
Offset Stripline |
The trace is covered by laminate on both sides. |
Edge Coupled Offset Stripline |
Consists of two controlled impedance traces placed between two planes. |
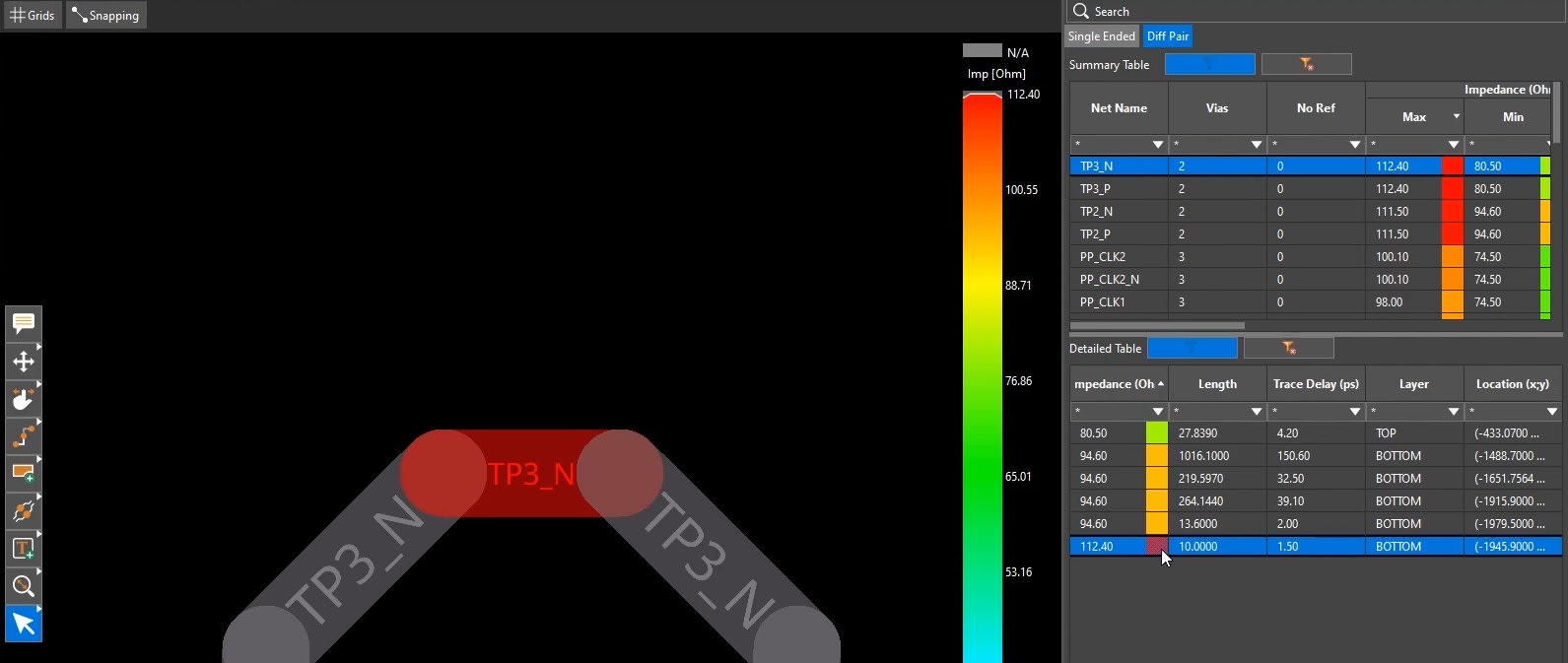
Apply Controlled Impedance Routing in OrCAD X
OrCAD X offers a comprehensive suite of tools designed specifically to help designers implement controlled impedance routing. These features allow for precise control over the impedance of your PCB traces.
OrCAD X Features for Controlled Impedance Routing
OrCAD X Feature |
Description |
How It Aids in Controlled Impedance Routing |
Allows designers to define and visualize the PCB stack-up, specifying material properties, layer count, and overall thickness. |
A well-defined stack-up ensures consistent impedance characteristics by controlling the distance between signal traces and reference planes, which is crucial for maintaining signal integrity. |
|
Design Rule Definition |
Enables the setting of electrical, physical, and manufacturing constraints, including those related to impedance, trace width, and via size. |
Establishing precise design rules ensures that all routing adheres to specified impedance requirements, reducing the risk of signal integrity issues. |
Provides immediate feedback on impedance values during the design process, allowing for quick identification and correction of impedance mismatches. |
Real-time analysis helps designers promptly address impedance discrepancies, ensuring that the final PCB meets the desired electrical performance standards. |
|
In-Design Coupling Analysis |
Assesses the coupling between adjacent signal traces to identify potential interference issues during the layout phase. |
By evaluating coupling effects within the design, this feature aids in adjusting trace spacing and routing to minimize crosstalk and maintain controlled impedance levels. |
High-Speed Routing with SI Analysis |
Incorporates high-speed routing capabilities alongside signal integrity analysis to optimize trace layouts for high-frequency signals. |
This integrated approach ensures that high-speed signals are routed with appropriate impedance characteristics, minimizing reflections and signal degradation. |
When you are working on high-speed, high-frequency circuits handling critical signals or data, signal integrity needs to be maintained throughout the operation. Controlled impedance routing is one of the best practices followed by PCB designers to ensure that signals reach the load from the source, without any loss or distortions. When circuit traces are impedance matched, the probability of signal integrity failure is reduced to a minimum. OrCAD X features ensure your PCB traces are properly impedance-matched for optimal performance. Learn more about OrCAD X and how it supports controlled impedance routing or check it out yourself and get started with a free trial.
Leading electronics providers rely on Cadence products to optimize power, space, and energy needs for a wide variety of market applications. To learn more about our innovative solutions, subscribe to our newsletter or our YouTube channel.