ECAD-MCAD Collaboration in OrCAD X
Key Takeaways
-
ECAD is used for designing printed circuit boards, ICs, and electrical-related data, while MCAD involves the physical enclosures, mechanics, materials, product design processes, dimensions, and tolerances.
-
Integrating MCAD and ECAD allows engineers to run both electronic and mechanical design processes simultaneously.
-
OrCAD X features enable efficient ECAD/MCAD integration, supporting real-time collaboration and change management.
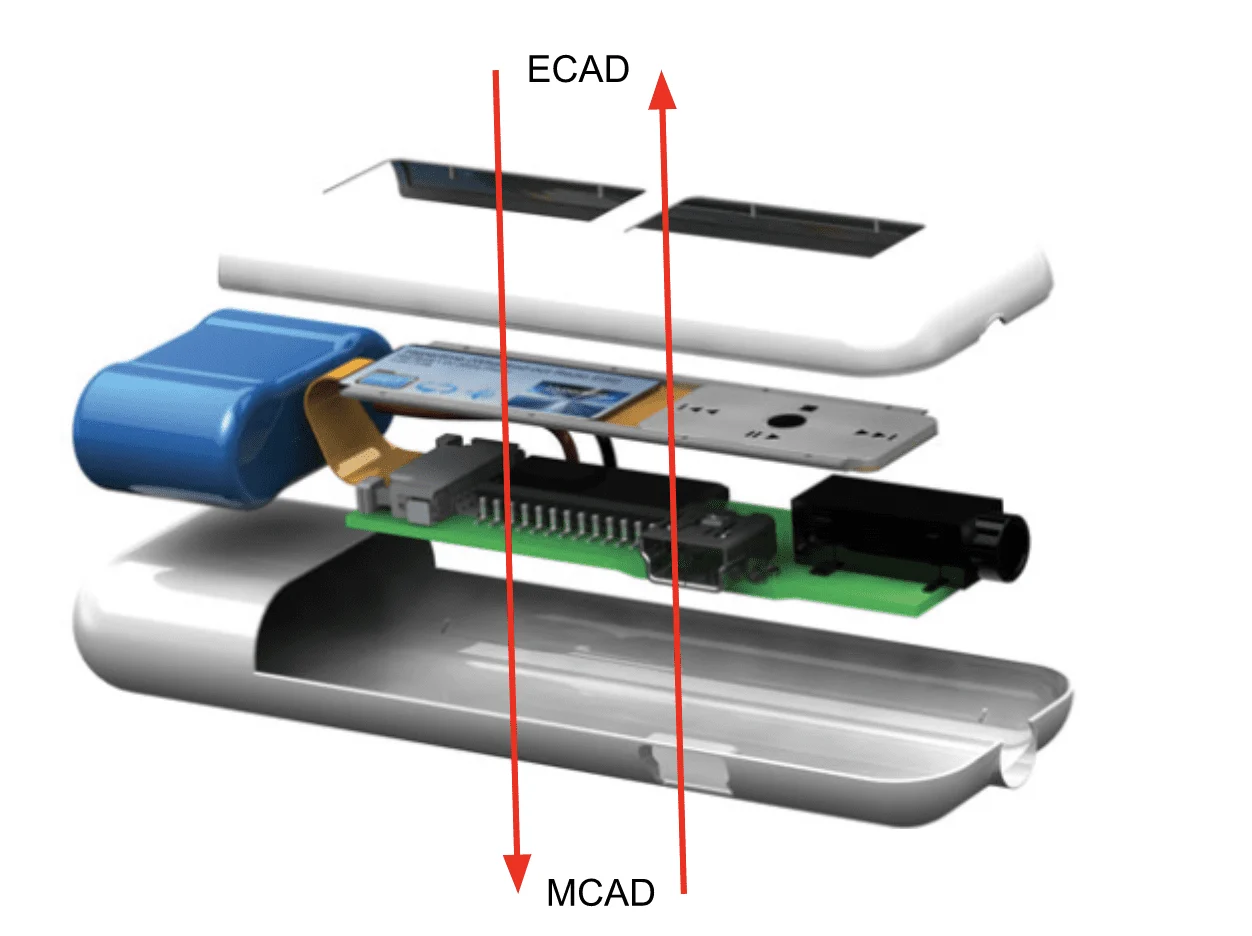
The co-design platform offered through MCAD/ECAD collaboration supports an efficient product design cycle
Electronic developments always face the constraints of form factor. The challenge is to achieve optimum design within a compact size and meet reliability, quality, and performance indices. To design such an electronics product, you need a domain with MCAD/ECAD collaboration capabilities. ECAD/MCAD co-design is essential to a modern product design cycle workflow, as it allows electrical and mechanical engineers to interact and synchronize throughout the design process. Read on as we discuss specifics for ECAD-MCAD co-design.
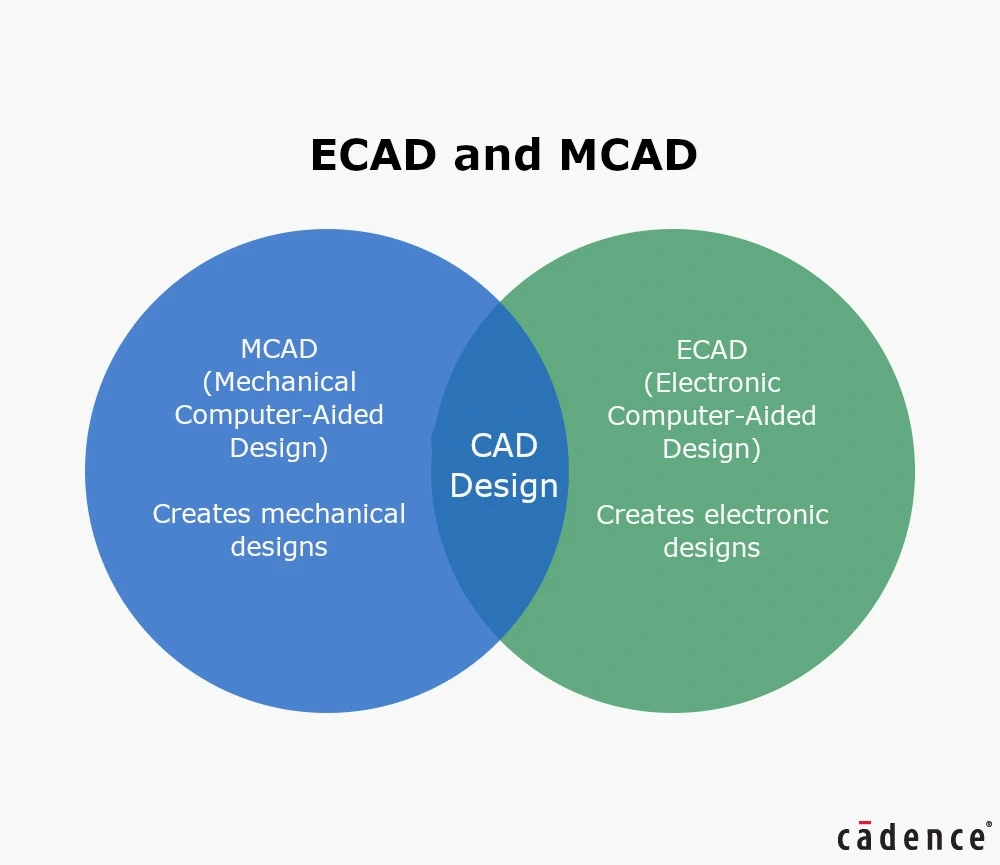
MCAD vs ECAD comparison.
How ECAD and MCAD Collaborate to Create Devices
Mechanical computer-aided design (MCAD) is a software-based design tool that helps engineers model their products. It incorporates information such as materials, product design processes, dimensions, and tolerances.
-
ECAD:Electronic computer-aided design, models the functional design of electrical and electronic systems. ECAD is used for designing printed circuit boards, integrated circuits, large electronic systems, and any design involving logic-driven electronics. It also provides a platform for electrical testing, and generating electrical-related schematics and other required electrical drawings.
-
MCAD: Drawings are significant in mechanical engineering. Engineers create 2-dimensional or 3-dimensional models when designing products to get accurate depictions of them. These drawings detail the specifications, which are required for product engineering and manufacturing.
Product Development With ECAD / MCAD Co-Design
Effective ECAD-MCAD collaboration is crucial for modern product design, where electronic and mechanical components must be integrated. The following are key ECAD / MCAD integrations essential to achieve efficient collaboration:
-
Bidirectional Data Exchange: ECAD-MCAD collaboration requires seamless data exchange between both domains. This ensures that changes made in one domain are automatically reflected in the other.
-
3D Visualization and Manipulation: The ability to visualize electronic designs in a 3D space with the mechanical data of the device is critical for verifying fit. Especially for dynamic materials that flex or move, being able to see how the electronics move in accordance is important.
-
3D Export Capabilities: For comprehensive analysis and simulation, being able to export 3D data is crucial. MCAD allows engineers to simulate the thermal and structural behavior of the electronic product under various physical conditions. Furthermore the testing of the electronic product, such as vibration testing or drop testing, can be performed with MCAD.
-
Design Sync: Improves predictability in the product cycle schedule, as the design is synchronized and it is easy to trace the modification from any domain.
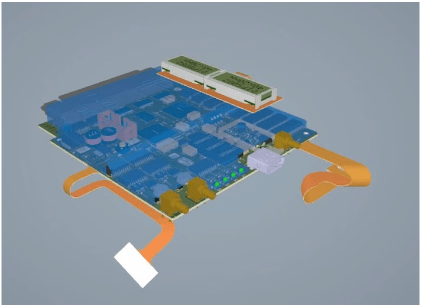
OrCAD X has a new 3D engine for resolving ECAD / MCAD conflicts, such as in a rigid-flex scenario.
ECAD/MCAD Co-Design Features
ECAD and MCAD software both support electronic product design in their unique ways. However, the existence of MCAD and ECAD as two separate platforms in product design presents some challenges.
-
ECAD fails to visualize the mechanical details of circuit design and cannot be depended on for structural and thermal analysis.
-
MCAD fails to include the functionalities and tools required for electronic design and cannot be depended on for electronic behavior analysis.
OrCAD X Features For MCAD/ECAD Collaboration
Collaboration between mechanical engineers and electrical engineers is necessary for developing an electronic product; a common platform is convenient to facilitate this process. Some features of MCAD/ECAD collaboration are:
Feature |
Description |
3DX Engine for Visualization |
Improves the visualization of rigid/rigid-flex designs, including material flexure and bend radii, aiding in manufacturability and reducing pre-production errors. |
Bidirectional Data Exchange |
Enables seamless synchronization of design data between ECAD and MCAD tools, ensuring consistent and up-to-date information across both domains. |
Intelligent Data Exchange |
Allows selective import/export of design elements between OrCAD X and SolidWorks, ensuring only relevant data is transferred, maintaining design integrity. |
3D Export Capabilities |
Supports exporting 3D design data in multiple formats, including rigid-flex designs when folded or bent, for further mechanical analysis in MCAD tools. |
Platform Connectivity |
Provides integration with major MCAD platforms like Autodesk Fusion, SolidWorks, CATIA, PTC Creo, and Siemens NX, facilitating real-time updates and collaboration. |
Change Management |
Tracks and manages design modifications with change history, acceptance, rejection, and reverting capabilities, reducing errors and maintaining design consistency. |
Real-Time Collaboration |
Enables push-and-pull changes with a single click, minimizing design errors and unnecessary iterations, enhancing collaboration between electrical and mechanical teams. |
3D Model Synchronization |
Synchronizes 3D models between ECAD and MCAD domains, ensuring a one-for-one match with the PCB database, crucial for accurate design representation. |
Mechanical Data Import |
Imports mechanical data such as board outlines, mounting holes, and keep-outs from SolidWorks into OrCAD X Layout, integrating mechanical constraints into PCB design. |
Design Data Export |
Exports complete board data, including 3D models, from OrCAD X to SolidWorks, enabling a comprehensive mechanical representation of the PCB design. |
Cloud-based MCAD/ECAD integration continues to support the engineering community to synchronize and collaborate. Cadence offers ECAD/ MCAD co-design platforms for collaboration between electronic and mechanical domains, enabling reduced electronic iterations, 3D viewing, and incremental design updates for improved design clarity.
To fully leverage the benefits of ECAD/MCAD collaboration, designers can rely on Cadence tools like OrCAD X to streamline their product development process. With advanced features such as 3D visualization, bidirectional data exchange, and real-time collaboration, OrCAD X ensures seamless integration between electrical and mechanical design teams. Explore how Cadence’s PCB Design and Analysis Software and the new OrCAD X platform can enhance your design workflow today.
Leading electronics providers rely on Cadence products to optimize power, space, and energy needs for a wide variety of market applications. To learn more about our innovative solutions, talk to our team of experts or subscribe to our YouTube channel.