PCB Design for Mechanical Engineers with OrCAD X Tools
Key Takeaways
-
Mechanical engineers ensure robust PCB designs that withstand stress, crucial in early development stages.
-
Integrating mechanical engineering in PCB design reduces costly modifications, speeding up production.
-
OrCAD X enhances PCB design for mechanical engineers by enabling seamless ECAD-MCAD data exchange.
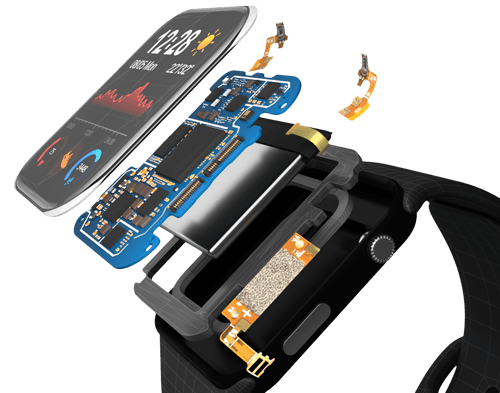
PCB design for mechanical engineers is enabled by new ECAD-MCAD Collaborative features within OrCAD X
At the beginning of product development, there’s a common tendency among innovators to prioritize the electronics and software aspects of PCBs, often overlooking the integral role of aesthetic and mechanical design. This oversight can lead to inefficiencies, causing unnecessary delays and financial oversights in the development process.
When various engineering fields merge they can better streamline processes, and elevate product quality. This synergy is especially crucial in PCB and electronic device design, as it involves a complex interplay of engineering disciplines working together. For this reason, PCB design for mechanical engineers is an important aspect that should be delved into —read on to learn why and how.
Tips For PCB Design for Mechanical Engineers
Role of The Mechanical Engineer |
Description |
Structural Integrity |
|
Thermal Management |
|
Streamlining Manufacturing |
|
Footprints for Unique Components |
|
Integration of 3D Component Shapes |
|
Board Shape Design |
|
Utilization of Advanced MCAD Tools |
|
Management of Trace Keepouts |
|
Influence of Industry Standards |
|
Benefits of Integrated ECAD MCAD Collaboration
From the very beginning, PCB design for mechanical engineers involves their close collaboration in the workflow. ;They play an important role in modeling the enclosure that will house the PCB. They also ensure that the PCB enclosure aligns with the design's intended function.
By working alongside electronic engineers during the PCB layout phase, mechanical engineers can provide insights into the best ways to arrange components to utilize space efficiently.
Structural Integrity Verification
Mechanical engineers ensure that the PCB and its components can withstand physical stresses such as shock, vibration, and thermal expansion. Early collaboration means these factors are considered during the circuit design phase, leading to a more resilient product. Throughout its operational lifespan, a PCB is subjected to a variety of harsh conditions. It's essential that the layout of the PCB is strategically engineered to endure the following environmental factors:
-
Temperature Extremes: The PCB must be capable of functioning effectively in both high and low-temperature environments.
-
Temperature Fluctuations: Regular cycling between temperatures should not compromise the PCB's integrity.
-
Environmental Humidity: Moisture in the environment can affect the functioning of the PCB, requiring designs that mitigate humidity-related risks.
-
Mechanical Stress: The PCB should be robust enough to handle shocks and vibrations without failure.
-
Particulate Exposure: Depending on the intended use and the IP rating of the product, the PCB must be resistant to contamination from both solid and liquid particles.
Streamlined Manufacturing Processes
When mechanical and electronic engineers collaborate from the outset, the entire design is more likely to be manufacturable without extensive modifications. This not only speeds up the time to market but also reduces the costs associated with iterative redesigns.
Innovative Solutions to Complex Problems
Bringing mechanical engineers into early discussions often leads to innovative solutions that might not occur in a siloed environment. This multidisciplinary approach allows for the cross-pollination of ideas, leveraging the strengths and perspectives of both fields to overcome design challenges.
How OrCAD X Enables Mechanical Engineers to Aid In PCB Design
OrCAD X offers robust ECAD-MCAD co-design capabilities, ensuring seamless collaboration between electrical and mechanical design teams. With bidirectional data exchange, real-time updates, and support for leading MCAD tools, OrCAD X minimizes design errors and iterations.
Advanced 3D visualization and platform connectivity enable effortless synchronization, optimizing PCB integration and ensuring design integrity across both domains.
OrCAD X ECAD-MCAD Collaboration Capabilities
Capability |
Description |
Collaboration with Mechanical Designers |
Facilitates the placement of connectors and components based on mechanical design requirements in Dassault Systèmes SOLIDWORKS, Autodesk Fusion, and other MCAD software. |
Effortless Synchronization |
Push and pull changes with a single click, supporting platform-to-platform or file-based data synchronization. |
Platform Connectivity |
Supports desktop data exchange and cloud connection to Autodesk Fusion and Dassault Systèmes 3DEXPERIENCE platforms. |
3D Visualization |
Advanced 3D capabilities to visualize and optimize PCB integration with mechanical enclosures early in the design process. |
Bidirectional Collaboration |
Send object changes from either domain to optimize electrical and mechanical integrity. |
Change History Management |
Ability to accept, reject, or revert changes using IDX, ensuring robust version control. |
MCAD Tools Supported |
Compatibility with Autodesk Fusion, Dassault Systèmes CATIA and SOLIDWORKS, PTC Creo, and Siemens NX. |
Visualization of Rigid/Rigid-Flex Designs |
New 3D engine enhances the visualization of rigid/rigid-flex designs, improving manufacturability analysis. |
3D Data Export |
Export 3D design data in multiple formats for ECAD and MCAD analysis, including folded or bent rigid-flex designs. |
SolidWorks Plugin |
Automates ECAD-MCAD collaboration between OrCAD X and SOLIDWORKS, enabling seamless data exchange and synchronization.. |
MCAD X Data Import/Export |
Import and export board outlines, mechanical mounting holes, and 3D models between OrCAD X and SOLIDWORKS. |
Integration Availability |
Available across all Allegro X and OrCAD X tiers, ensuring accessibility to all users. |
See our “Seamless ECAD and MCAD Collaboration” webinar for more information or the ECAD-MCAD Co-Design for Success datasheet.
For designers focused on PCB design for mechanical engineers, integrating mechanical considerations early in the design process is crucial for ensuring structural integrity and manufacturability. With real-time data synchronization, 3D visualization, and support for leading MCAD platforms, OrCAD X ensures your PCB designs meet all mechanical and functional requirements from the outset. Explore how Cadence can enhance your design process with PCB Design and Analysis Software and discover the capabilities of OrCAD X today.
Leading electronics providers rely on Cadence products to optimize power, space, and energy needs for a wide variety of market applications. To learn more about our innovative solutions, talk to our team of experts or subscribe to our YouTube channel.