PCB BOM Management for Engineers and Designers
Key Takeaways
-
Understand the essential elements of a Bill of Materials that impact design, sourcing, and production.
-
Learn step-by-step best practices for engineering BOM management and PCB BOM management.
-
Through real-time data, OrCAD X improves BOM accuracy, risk mitigation, and part selection.
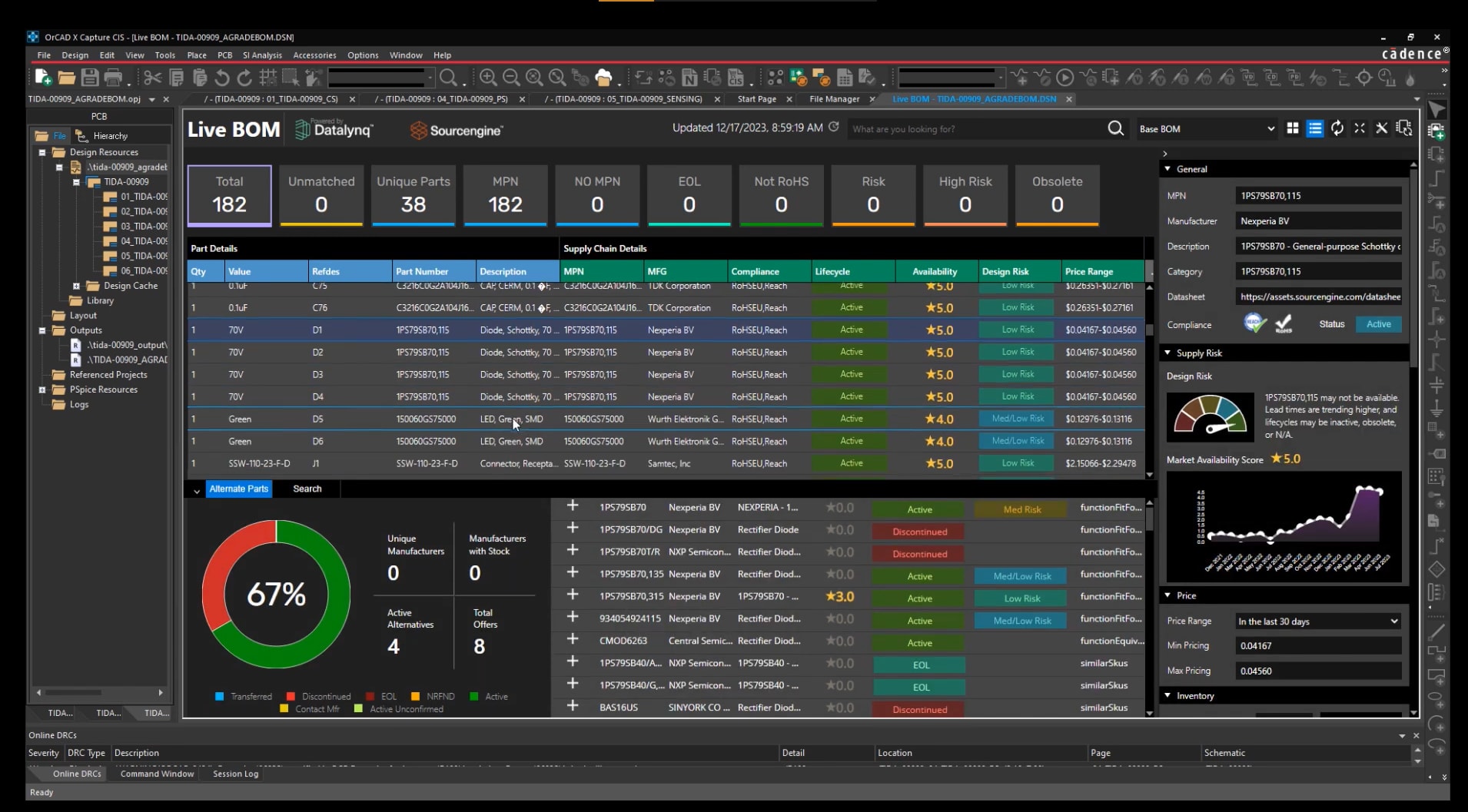
Engineering BOM management oversees all product data across its lifecycle. PCB BOM management is a subset that encompasses the coordination of personnel, processes, and technology to handle a company’s BOMs efficiently as they relate to printed circuit boards (PCBs). PCB BOM management is essential for linking various departments required for product development, from engineering to the supply chain.
Good PCB BOM management can facilitate cross-departmental collaboration, streamline change and configuration management across varied BOM structures, and ensure faster time to market by providing early visibility to stakeholders and enabling access to information at the onset of product development.
Key Elements of a PCB BOM
To ensure efficient design, procurement, assembly, and manufacturing for PCB BOM management, an optimized Bill of Materials (BOM) should include the following elements:
-
Accurate Part Numbers: Uniquely identify each component across systems. Ensure traceability throughout the product lifecycle.
-
Detailed Part Descriptions: Clarify component usage, features, and functional roles. Prevent ambiguity between similar components.
-
Supplier and Manufacturer Information: List approved vendors and original manufacturers. Support strategic sourcing and vendor negotiations.
-
Quantity per Assembly: Define how many units of each component are necessary per product. Enable accurate cost estimation and procurement planning.
-
Part Classifications or Categories: Organize parts into logical groups for easier management. Facilitate standardization and reuse of standard components.
-
Lifecycle Status: Identify whether parts are active, obsolete, NRND (Not Recommended for New Designs), or EOL (End-of-Life). Help avoid design disruptions and unplanned redesigns.
-
Compliance and Regulatory Data: Ensure conformity with standards like RoHS, REACH, and conflict minerals. Prevent the use of restricted or banned substances in production.
-
Alternate or Equivalent Parts: Suggest interchangeable components that match form, fit, and function to reduce risk during shortages or end-of-life transitions.
-
Component Risk Assessment: Highlight potential risks such as obsolescence, limited sources, or poor availability. Inform proactive design and procurement decisions.
-
Inventory Availability: Show current stock levels from suppliers and distributors. Help plan for lead times and avoid production delays.
-
Pricing and Price History: Include real-time and historical cost data per unit, support cost optimization, and budget tracking.
-
Datasheet and Documentation Links: Directly access technical specifications and reference materials. Assist in validation, testing, and regulatory review.
-
Lead Time Estimates: Reflect average delivery time frames from suppliers. Enable better production and inventory scheduling.
Basic Steps Outlining Engineering BOM Management
Step |
Action |
Action Description |
1 |
Establish BOM Requirements |
Identify the need for a new or updated BOM based on design, material, or process changes, and assess resource capacity. |
2 |
Create a Structured BOM |
Create a detailed BOM with a clear hierarchy, accurate descriptions, part numbers, and quantities. |
3 |
Implement BOM Management Software and Version Control |
Use a version control system to track BOM changes over time, ensuring accuracy and reducing errors. Utilize specialized software for automated version control, collaboration, and integration with other systems. |
4 |
Document Component Information |
BoMs should include comprehensive component specifications, materials, dimensions for manufacturing reference, and alternatives for specific materials in case of supply chain issues. |
5 |
Standardize Naming Conventions |
Use clear and consistent naming conventions for components to reduce confusion. |
6 |
Review and Approve BOMs |
Conduct thorough reviews and obtain stakeholder approvals to ensure BOM accuracy and completeness. |
7 |
Outline Change Control Procedures |
Develop procedures for managing, reviewing, and approving BOM changes. |
8 |
Audit and Adjust BOM |
Regularly audit the BOM to correct discrepancies or outdated information. |
9 |
Apply Continuous Improvement |
Evaluate and improve the BOM management process based on feedback and practice changes. |
10 |
Train Personnel |
Provide training on maintaining BOM accuracy management tools as necessary. |
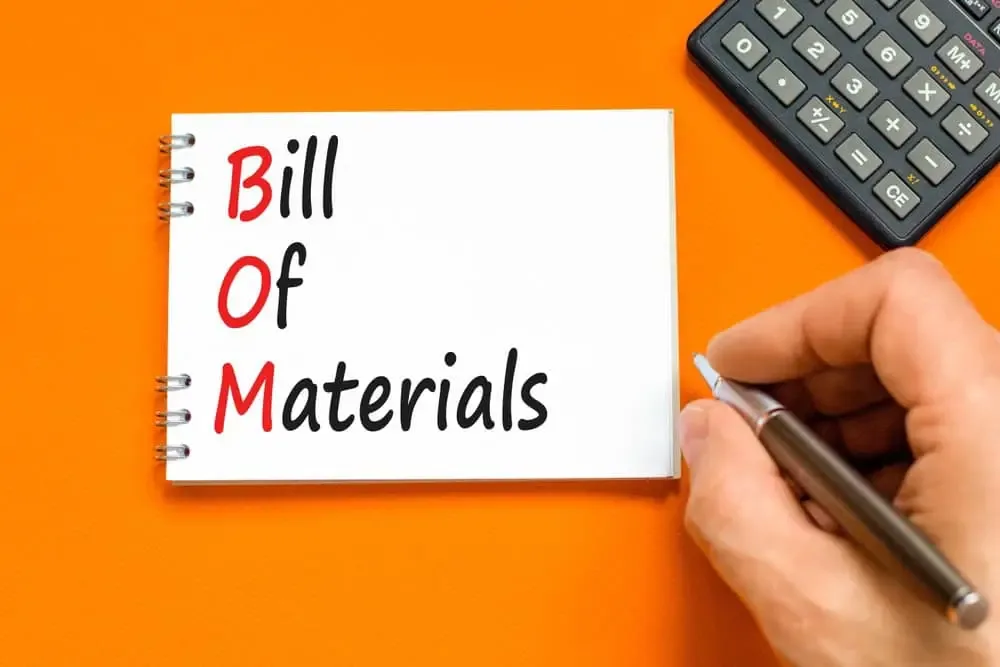
Engineering BOM management requires intelligent software.
What Goes Into Effective BOM Inventory Management?
PCB BOM management involves creating a BOM tailored to specific phases of the product lifecycle and stakeholders' needs. It is crucial to use a standard format to ensure consistency, clarity, and ease of communication across departments. Employing BOM management software is essential for automating and optimizing the process, offering features like version control, real-time collaboration, and integration with other systems.
An effective BOM includes several key elements that serve specific purposes throughout the product lifecycle. For example, part numbers and descriptions ensure clarity in procurement and assembly, and supplier and manufacturer details streamline sourcing. Quantities and reference designators assist in accurate manufacturing, and fields like lifecycle status and compliance ensure regulatory alignment and reduce risk. Collectively tracking these attributes forms the backbone of PCB BOM management. |
Good management also includes determining access controls, conducting regular audits, applying continuous improvement methods, and training personnel. Additionally, simplifying the BOM data by breaking down components into their simplest items and reducing unnecessary complexity further contributes to well-managed, effective PCB BOM management.
Key aspects of engineering BOM management include:
-
Materials Planning: Use the BOM as a guide to outline product structure and material requirements.
-
Inventory Tracking: Includes monitoring stock levels within the supply chain, including quantities on hand, in transit, and on order, to avoid shortages or excesses.
-
Demand Forecasting: Tying inventory management to production schedules and product demand to ensure materials are available when needed, minimizing surplus inventory and costs.
-
Real-time Visibility: Implementing technologies for immediate insight into inventory levels, aiding timely decisions on reordering materials, and adjusting stock based on demand shifts.
-
Cost Control: Managing inventory-related costs, focusing on reducing expenses tied to storage, handling, and risks of obsolescence or discontinuation.
OrCAD X Live BOM Allows for Efficient Engineering BOM Management
Live BOM in OrCAD X offers engineers a tool for managing supply chain risks and making informed commercial decisions by providing visibility into market intelligence scores for electronic components, assessing design risk, market availability trends, and substitution options among its key features.
With Live BOM, engineers access a dataset for each part in their design, including manufacturer details, part numbers, lifecycle status, compliance, risk, pricing, inventory, and key component properties. The interface allows for filtering and ordering the BOM to focus on parts needing attention, displaying comprehensive information like datasheet links, design risk assessments, market availability, price history, and inventory tracking.
Live BOM Enables PCB BOM Management Through Alternate Part Suggestions
One of Live BOM's standout features is its ability to suggest alternate parts that match the original components' form, fit, and function, allowing for substituting high-risk components with lower-risk alternatives. This capability is crucial for updating projects based on designs from previous years, ensuring lower supply chain risk, maintaining production lines, securing product availability, and enabling more stable cash flows. Live BOM transforms the BOM management process, turning potential challenges into opportunities for strategic supply chain and design decisions.
Effective PCB BOM management and engineering BOM management are critical to minimizing design risks, streamlining sourcing, and accelerating time-to-market. Cadence's OrCAD X platform equips designers with powerful tools to manage complex BOMs across the entire product lifecycle. Ready to optimize your BOM process and future-proof your designs? Explore the OrCAD X platform or start your free trial of OrCAD X today.
Leading electronics providers rely on Cadence products to optimize power, space, and energy needs for a wide variety of market applications. To learn more about our innovative solutions, subscribe to our newsletter or our YouTube channel.